Powerful and durable
A brushless DC motor ( BLDC motor for short) is powerful and particularly durable, as there are no brushes or other wearing parts in the mechanical structure. Above all, the high-quality ball-bearings in the armature shaft ensure a long service life. The compact case, which fits into almost any small installation space, has a higher power density compared to brushed DC motors.
Product Filter
No match for the required drive component here?
Oh, then we have not yet included the right product for your requirement criteria in our online product database
But maybe in our warehouse after all!
We have almost countless types of DC motors and drive components on offer and many are even available in stock. Or we can assemble the complete drive system specifically for your application. We would be happy to work with you to consider which configuration might provide the optimal drive. Just talk to us directly!
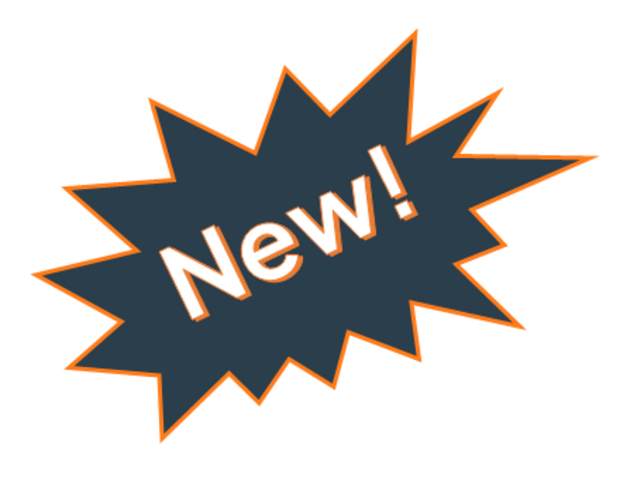
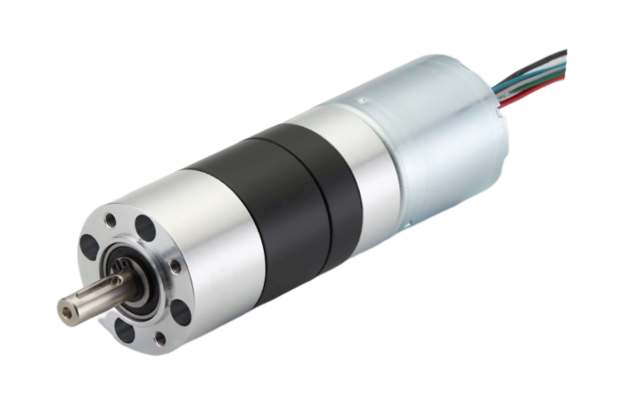
New in the product catalog | BLDC motor with new planetary gear
The new P042066 series is a BLDC motor equipped with a new planetary gear. The advantages of the new planetary gear in its two variants with double ball bearings and reinforced planetary gears, as well as a variant with helical-toothed plastic gears in the first stage, are explained in detail in the planetary gear motors section.
Advantages of this BLDC planetary gear motor P042066
- In the elongated form, the larger part is the active part.
- Short response time
- Low moment of inertia
- High rotation speeds
- Lower power consumption
- High efficiency over long lifetime
Areas of application
- In high-precision applications that require low gear backlash, e.g. in the positioning of laser optics and mechanical processing
Why does a manufacturer need this motor?
- Motor is longer overall (66 mm) with this planetary gear, which enables higher rotation speeds. This results in improved rated power.
- If the diameter of the motor had been increased, the torque would be increased, but so would the breakaway torque. This would result in increased current consumption and lower rotation speeds. This would be a disadvantage for applications that require higher rotation speeds.
- The reduced breakaway torque also means that shorter response times can be achieved, which is necessary in some designs. Especially for electronically controlled BLDC motors with many changing requirements.
Our best BLDC motor for you in just three steps
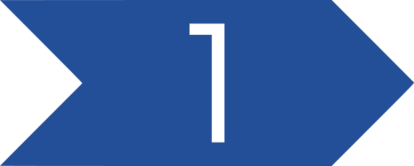
You need a DC geared motor for your application.
Your main criterion: the motor should be as low-wear as possible.
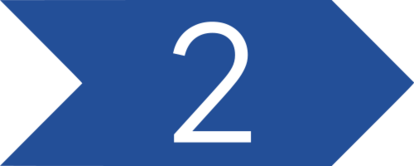
We will show you the optimum BLDC motor for your specification. You will receive all motor dimensions and detailed drawings as well as the desired characteristic curves. We will also test the motor extensively on our drive test bench.
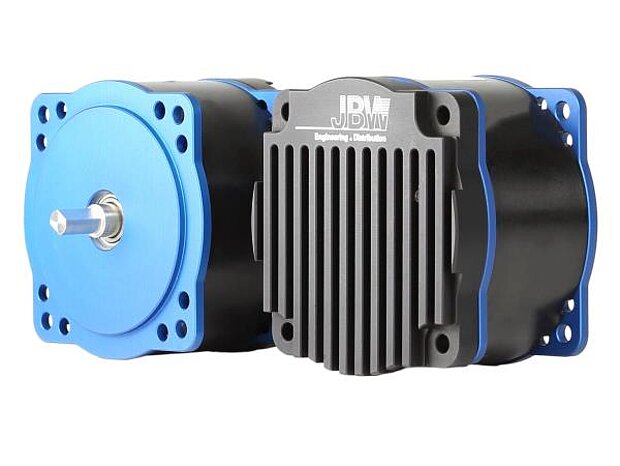
High-torque BLDC motor
Powerful, precise and cogging-free
The new technology of this high-torque BLDC motor makes it a reality: very high efficiency with low dimensions and weight, extremely smooth, jerk-free and low-noise running and a long service life. This patented motor technology combines all the advantages of classic DC motors with fully electronic commutation. The integrated electronic control with encoder ensures a wide range of applications with low implementation effort.
This brushless motor operates according to the patented axial flux double disk rotor principle with continuous commutation. The fully integrated electronics, which are matched to the motor characteristics, are responsible for motion control. The geared motor achieves an exceptionally high torque density of 0.5 Nm with high overload capacity and adjustment dynamics. A specially developed air armature principle is used instead of the usual slotted armature. This guarantees complete freedom from cogging torque and thus ensures outstanding running smoothness and fast, precise fine positioning.
Special advantages of the high-torque BLDC motor
Small and compact, the high-torque BLDC motor is also stable and durable. Thanks to its design, it has high mechanical rigidity and no problems with heat dissipation from the winding. The design of the high-torque BLDC motor deliberately avoids self-supporting windings and components that cause instability or a tendency to vibrate. All elements are connected to the motor housing or the motor shaft in a large and stable manner.
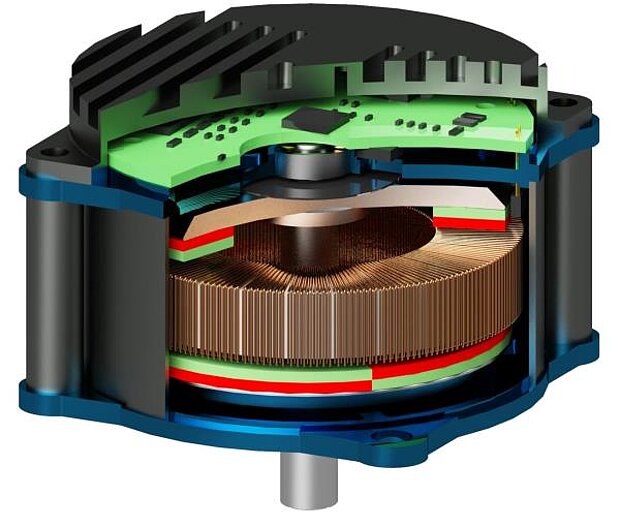
Torque
Maximum torque due to ring-shaped armature with large effective radius and constant load angle
Cogging-free
The ring-shaped air armature with continuous commutation and therefore constant load angle results in a constant dynamic torque regardless of the angle of rotation.
Synchronization
As there are no torque and load peaks depending on the angle of rotation, the high-torque BLDC motor achieves excellent synchronization.
Control quality
Thanks to the enormous torque density and the specially developed control IC, the response times are just a few nanoseconds.
Ready for operation without additional electronics
In addition to commutation, the fully integrated control electronics can handle many control tasks for standard applications as well as optional communication via various bus systems (motion controllers). In many cases, additional control electronics can be dispensed with entirely.
Endurance run
If the high-torque BLDC motor is supplied with voltage, it runs continuously like a normal DC motor.
Control signal
Various parameters such as rotation speed, torque, direction of rotation, etc. can be specified via control inputs.
Data bus
For demanding motion sequences, the high-torque BLDC motor communicates with a higher-level control unit via a standard data interface (data bus).
In addition to the electronic commutator, which is controlled by a programmable logic (CPLD), a microcontroller is integrated in the motor, which in the standard version takes over the direction control, PWM speed control with ramp functions for acceleration and deceleration as well as various protective functions and error analysis, among other things. An incremental encoder with pulse counter is also included, allowing the speed to be controlled as well as the position in multiturn mode. By modifying the firmware, it would be possible, for example, to control an oscillating movement, such as that required for the windshield wiper drive, over many motor revolutions (gear input) despite the large gear reduction.
A single additional position sensor on the output - ideally with a switching point in the middle of the movement - would be sufficient to detect the absolute position when switching on (or during basic initialization) and then perform a sinusoidal-like movement control at the reversal points. In addition to this smart motion sequence, wear on all moving parts and current peaks are also reduced. The additional position encoder can be connected directly to an input line of the integrated motor electronics, so that no other external control elements are required apart from a start-stop line.
We are happy to check other special functions on request.
The high-torque BLDC motor is available as a motor without gear. We also supply it combined with a planetary gear as well as with a spur gear. Further approvals can be optionally configured to suit the specific application. It is only available in this size.
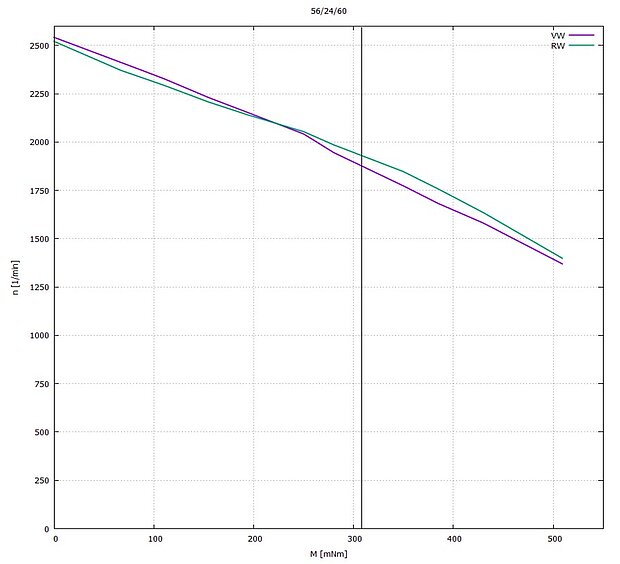
Torque/rotation speed characteristic curve with PWM = 100 % (forward/reverse)
We have the CAD data and the motor characteristics for all our geared motors. The entire characteristic curve field of the high-torque BLDC motor shown here can be used for short periods. The continuous torque must be limited to the limit shown at 0.31 Nm due to the heat development at 25 °C ambient temperature. A power limit becomes effective for torques above 0.5 Nm.
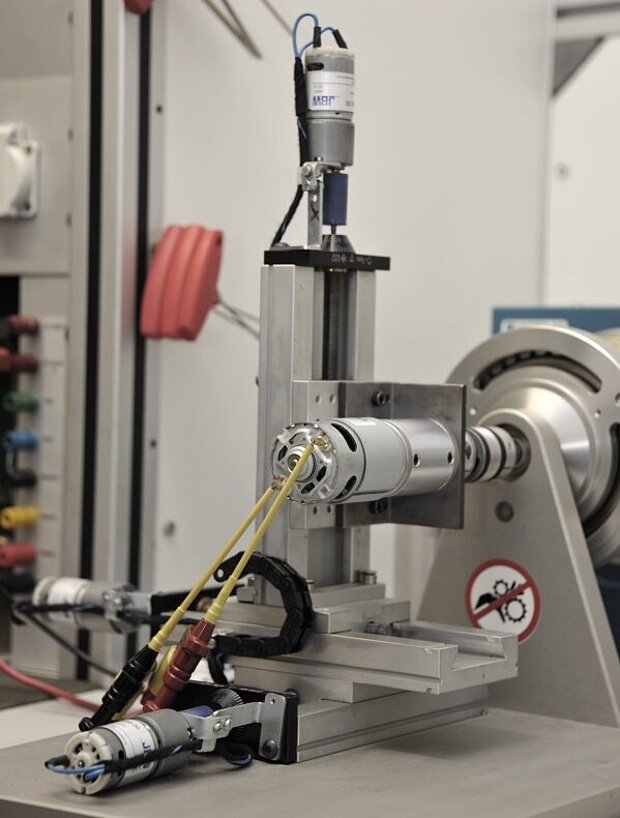
BLDC motor - the right choice
Our engineering-team is ready to support you in selecting the right DC geared motor. With help and advice! We have a lot of experience in determining which motor type offers the most efficient benefits in your specific application. Is it really a BLDC motor or perhaps a more cost-effective worm gear motor that does away with brakes thanks to its self-locking function? We will be happy to test your motor on our drive test bench to verify your required performance criteria so that you can be sure you have made the best choice. Performance data as well as robustness and reliability and, last but not least, the costs for the entire drive system must match your product.
We offer the right engineering services for special requirements
- For example, we use 3D printing to produce small housings for critical plug connections.
- We assemble components for quick installation at your site in advance with the DC motor before we deliver everything to you on time.
- We provide you with suitable DC motors for qualified prototyping.
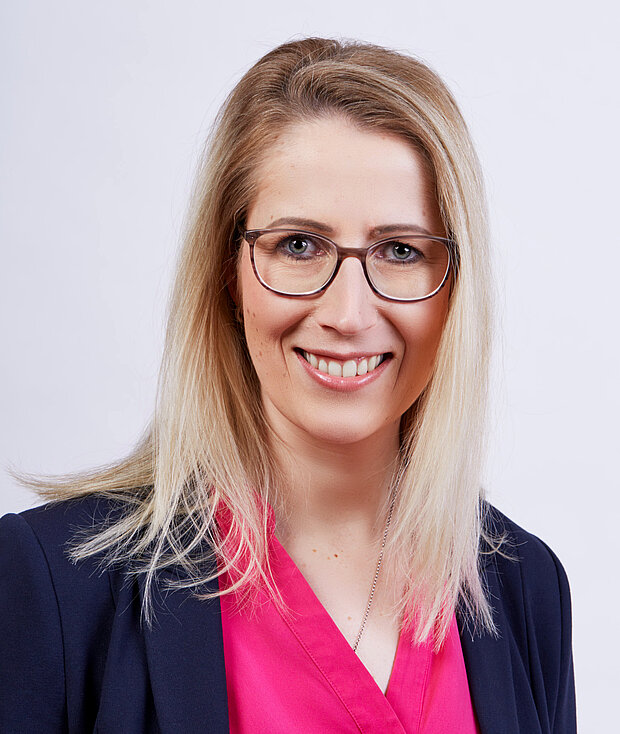
BLDC motor and high-torque BLDC motor | Your questions & our answers
A BLDC motor is a so-called brushless DC motor. This is a case of electric motors in which commutation takes place electronically. Therefore, no sliding contacts are required (also known as brushes).
With brushedDC motors, the mechanical carbon brushes supply the current through the commutator to the coils on the rotor. Carbon brushes can be thought of as mechanical switches that allow current to flow through the appropriate windings via sliding contacts on the rotor and control generated magnetic fields so that the armature rotates in the desired direction.
But as the name suggests brushlessDC motors do not use brushes. So how is current transmitted to the rotor coils in a brushless motor? A BLDC motor does not need this transmission at all, as the coils are not located on the rotor; instead, the rotor is a permanent magnet. In a BLDC motor, the coils do not rotate because they are mounted on the stator, the motor pot. Because the coils do not move, no brushes or commutator are required. Instead, a controller is required that uses sensors to determine the position of the rotor and performs commutation, i.e. current always flows through the correct winding.
The main criteria for differentiation
Brushed DC motor
- Permanent magnets in the motor pot
- Winding on the rotor
Brushless DC motor
- Permanent magnets on the rotor
- Winding in the motor pot
This engine is manufactured exclusively in Germany. This means short distances. But we also deliver abroad
JBW maintains a large warehouse in Munich so that DC motors are available quickly. We guarantee delivery times for framework agreements with agreed quantities and delivery times.
From us at JBW GmbH, because we are always happy to support our customers - with advice, engineering and even prototyping. Please send us an e-mail to info@elektromotore.eu with your contact details and the application for which you would like to use the high-torque BLDC motor.
Yes, JBW offers various control systems that perform functions ranging from simple commissioning to motor monitoring and motor control. And if the right controller is not available as standard, we work closely with our supplier, who can implement almost all requirements.
A BLDC motor designed for 24V can be damaged at higher voltages. A slight increase of 2 to 3 Voltage is conceivable, but should be tested in the specific application.